Liquified Petroleum Gas (LPG) is a mixture of several hydrocarbons (mainly propane and butane) that is stored in a compressed and cooled liquid form. Since LPG is a gas in the atmospheric condition, to store it in liquid form, it needs to be kept at a specific pressure and temperature. For example, propane stored at 20°C must be kept at a minimum pressure of 1000 kPa. Due to the volatile nature of LPG, the design of a fire protection system for its storage and transportation equipment presents a unique challenge. The most common cause of LPG Vessel fire are:
- Failure of the pressure relief valve on a storage vessel to activate at its set pressure. The built-up pressure would eventually cause the vessel to rupture and explode.
- an external source of fire starting could heat the vessel causing a change in the storage properties of the LPG as well as a loss in vessel integrity, which would once again cause a vessel rupture.
- A leakage occurring through a weak joint in the vessel, which would cause LPG spill on the ground that rapidly vaporize, form a cloud, and ignite. Lack of scheduled preventive maintenance and periodic inspection for LPG Containers/vessel is the reason behind such a failure scenario.
There are design challenges unique to each LPG Storage or handling facility that need to be considered in the design and installation of fire suppression systems for such facilities. So how do we account for these challenges in a fire suppression system for LPG floating stations and rail cars? Well, when customers come to us at Rotaflow for help with their LPG floating stations, we have a few options we usually consider.
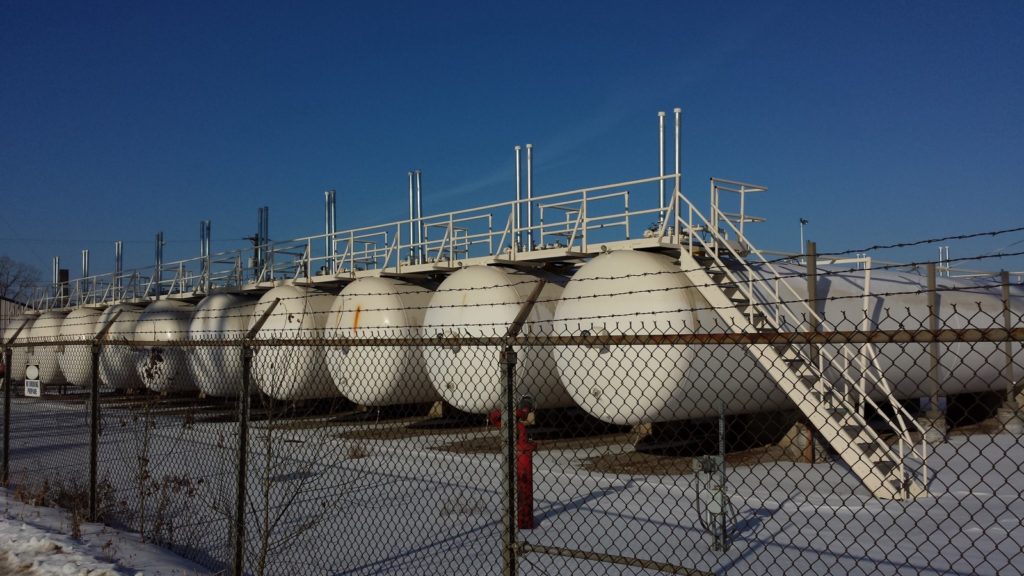
Fire prevention and protection requirements for LPG storage, handling, transportation, and use, are covered by NFPA 58. In the province of Alberta, The Alberta Boiler Safety Association (ABSA administers Alberta’s pressure equipment safety programs under the Safety Codes Act, lists NFPA 58 as an enforced standard. NFPA 58 itself refers to NFPA 15 (Standard for Water Spray Fixed Systems for Fire Protection) when it comes to design specifications for active water-based fire suppression systems for LPG storage, handling, transportation. This set of codes dictates the minimum standards required for the before-mentioned fire suppression systems.
When it comes to LPG railcar stations, A deluge system or a fire monitor system are the two co common options. The layout of your facility will help you determine which of these systems works best, or you may even need a combined system. A fixed water spray system (Deluge system) can be installed under the roof /canopy covering the rail car stations. An alternative choice of fire suppression would be to install fire monitors on both sides of the rail cars on the ground or on elevated platforms (should an obstruction prevent water from reaching the surface of the protected area).
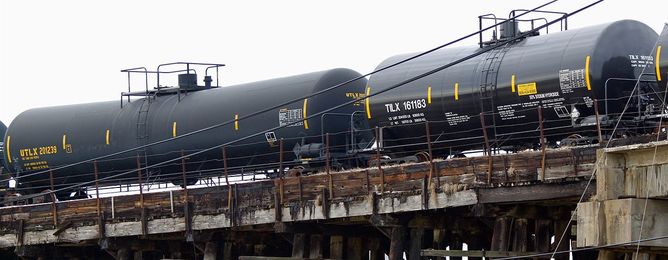
The water spray fixed suppression systems designed per NFPA 15 also rely on an automatic fire detection system for early detection of rising in vessel external temperature and LPG vapour formation due to a potential spill/leakage. Typically, a combination of Heat/IR detectors and gas detectors would be required to be installed for the rail car stations to complement the active fire suppression system. NFPA 15 also requires that these systems use both manual and automatic means of activation for the suppression systems.
The fixed water pray system systems will achieve the goal of fire suppression through the application of two different mechanisms:
- Surface cooling
- Vapor mitigation.
The surface cooling mechanism involves the constant application of water to the surfaces of LPG vessels and equipment with the main goal being to cool the equipment and vessels to slow the rate of heating. This mechanism protects the storage vessels from an external fire that has not yet compromised the vessels’ integrity to ensure they can withstand the duration of the fire. Research provided by NFPA 15 shows that proper surface cooling can reduce the rate of heat transfer to about 30% of the rate an unprotected vessel would experience. This slower rate of heat transfer means your assets can last longer before failing in an emergency, and it provides more crucial time to allow the fire to be controlled or extinguished. Surface cooling also has the benefit of reducing the potential for static electricity, which adds another layer of protection from potential ignition sources. NFPA 15 requires that systems using this mechanism for fire control are designed to sufficiently wet the entire surface of the LPG storage vessels. This requirement however means that you would most likely need nozzles directing water to both the top and bottom of the railcars, as their curved surface would prevent sufficient run down to cover the bottom surface of the car. For this mechanism to be used to its fullest effect, the system should include a heat detection system or similar activation mechanism so that it can automatically activate when it detects LPG vessels heating to dangerous levels.
Vapour mitigation involves the dispersion of the LPG vapour through sufficient water flow dispersed through the vapour. This mechanism occurs after a vessel has lost its integrity and has begun leaking vapours. If the desired water flow is achieved, it pushes the gases and stimulates airflow, which will reduce the concentration of LPG vapour in the air to be below its flammable limit. This effect will either prevent the vapours from igniting or suppress the resulting fire after ignition has occurred. For this to be achieved, systems should be designed so the water spray would cover any equipment that could potentially leak LPG vapours. This means that any hoses, pumps, or connecting valves would need to be covered by the system in addition to the railcars. The system should be designed to have a vapour detection system as one of the means of activation since it could prevent a fire from occurring in the first place by dispersing vapours that have not yet ignited. The vapour detectors should be calibrated for whichever LPG product your facility contains. It should be noted however that this mechanism can only be achieved in an open space where sufficient airflows can be achieved from the water spray, meaning if the area is under a canopy, it should be designed with enough open walls to allow the required airflow.
As you can see, a well-designed fire suppression system can play a crucial role in protecting your assets in the event of a fire. Whether they are used to keep the disaster under control or prevent one from happening in the first place, these systems are a crucial feature for safe LPG facilities. Remember, however, that fire suppression systems should always be your last line of defence against fire hazards. Prevention through proper design of process, process control systems, alarm and operator intervention, safety instrumented systems, physical protection devices like relief valves, and physical containment of the asset can prevent disaster before it ever has a chance to happen. If you need a fire suppression system built for your LPG facility, contact Rotaflow and our team can design a system that meets your facility’s needs.